TOVA is the first architectural construction in Spain located in the facilities of IAAC Valldaura Labs, Barcelona, built with a Crane WASP, the architectural 3D printer. The construction can be completed within weeks using 100% local materials and local labor, zero waste and a close to virtually zero carbon emission footprint. This manufacturing system can be used anywhere in the world and can help to housing emergencies. The project has been developed by the team of students and researchers from the 3D Printing Architecture (3dPA) postgraduate program of the Institute for Advanced Architecture of Catalonia (IAAC).
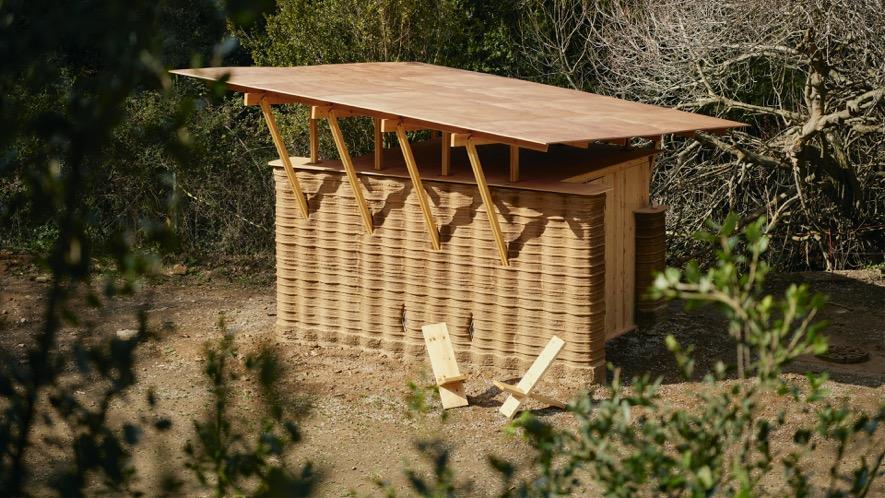
The Institute for Advanced Architecture of Catalonia (IAAC) presents the first building made with earth and a 3D printer in Spain, a project born from the ongoing research conducted by IAAC to find new ways of facing the social and environmental challenges of the future through its various education and research programs. The construction has been carried out at the Valldaura Labs facilities, on the outskirts of Barcelona. It is a prototype that represents the bridge between the past — vernacular earthen architecture — and the future — large scale 3D printing technology — which will not only serve to change the architecture of the future, but will also be very useful when facing the current climate and housing crisis across the globe.

The project has been developed by the 3DPA postgraduate research program at the IAAC. The objective of this course is to train young architects and academics for the future of construction and to explore the possibilities of 3D printing in this sector.
‘TOVA’ is the beginning of a larger project in collaboration with WASP in which a complete house made with 3D printing technology is projected.
Fast, waste-free and adaptable construction
It is the first building of this type in Spain and stands out for being one of the most sustainable and environmentally friendly construction forms that can be applied today. The construction took 7 weeks time to complete, a Crane WASP, the architectural 3D printer and km zero materials.
During the entire construction process, zero waste is generated, as the materials were sourced within a 50 meter radius. The structure is made of local earth, mixed with additives and enzymes, to ensure the structural integrity and material elasticity necessary for the optimized 3d printing of the house. The foundation is made of geopolymer and the roof, wooden construction.
To ensure the longevity of the material in resistance to weather, a waterproof coating is added using raw extracted materials such as aloe and egg whites.
The design of the building takes into account the climatic conditions of the Mediterranean: the volume is compact to protect from the cold in winter, but expandable during the other three seasons of the year, allowing the use of the immediate outdoor surroundings. The walls are made up of a network of cavities that contain airflow and allow great insulation to prevent heat loss in winter and protect from solar radiation in summer.
It is a near-zero emissions project: its shell and the use of an entirely local material allow the reduction of waste, making it a pioneering example of low-carbon building, given that current construction methods are responsible for 36 % of CO2 emissions.
The possible applications of this construction model are endless; from homes, to public spaces, interiors and exteriors. In combination with other construction systems, it can accommodate complex and innovative buildings that would reduce the environmental impact that construction currently entails.
Homes to face the housing emergency crisis of today and the future
The project was conceived as a prototype for sustainable housing that could be built anywhere in the world. This promising technique opens the door to quickly solving problems of access to housing in vulnerable areas or temporary settlements, offering new solutions for the creation of more sustainable and affordable spaces.
3D printing (or additive manufacturing) is a great example of km zero construction, as the construction work can be done 100% with local materials and labor. In addition, the printing system allows highly customizable houses for different use cases; such as communities of homes and services that can be rapidly created using this technology anywhere.
IAAC responds with this and other projects to increasingly serious climate and migration emergencies, providing new solutions that contribute positively to the global housing emergency problem that will have to be faced in the future due to large migrations or natural disasters. The use case of this rapid construction method can be a solution for increasing spaces that require emergency response for housing solutions of masses such as communities for asylum seekers.
Project credits
IAAC Team
Edouard Cabay, Alexandre Dubor, Lili Tayefi, Vincent Huyghe, Ashkan Foroughi, Eduardo Chamorro Martin, Elisabetta Carnevale, Guillem Baraut, Gloria Font basté, Nikol Kirova, Francesco Polvi, Bruno Ganem Coutinho, Marielena Papandreou and David Skaroupka.
Project partners
Colette, WASP, UN-Habitat, SOCOTEC, LaSalle, SmartCitizen, Scuares, Vervictech and Living Prototypes Research Innovation
Researchers
Adel Alatassi, Aslinur Taskin, Charles Musyoki, Deena El-Mahdy, Eugene Marais, Hendrik Benz, Juliana Rodriguez Torres, Leonardo Bin, Mariam Arwa, Al-Hachami, Marwa Abdelrahim, Mehdi Harrak, Michelle Bezik, Michelle Antonietta Isoldi Campinho, Mouad Laalou, Nareh, Khaloian Sarnaghi, Nawaal Saksouk, Orestis Pavlidis and Seni Boni Dara.
Acknowledgements
Areti Markopoulou, Mathilde Marengo, Ricardo Mayor, Shyam Zonca, Pilar Xiquez, Ariannet Arias, Gabriel Frederick, Nicolas Rodriguez, Daniela Figueroa Claros, Laura Ruggeri, Xavier Molons, Jorge Ramirez, Jordi Guizán Bedoya, Massimo Visiona, Lapo Naldoni, Massimo Moretti and Francesca Moretti.
3DPA participates in the Living Prototypes collaborative project and is supported by the Federal Research Institute for Construction, Urban Affairs and Spatial Development of the Ministry of the Interior, Construction and Community with funding from the Zukunft Bau research innovation program.